Selection of Oxidant for Oxygen-enriched leaching
2020-10-09 10:26Introduction:Selection of Oxidant for Oxygen-enriched leaching Oxygen required for cyanide leaching is usually supplied by several oxidants: air, oxygen, hydrogen peroxide, and calcium peroxide. Table 8-12 lists the roles and characteristics of differe
Oxygen required for cyanide leaching is usually supplied by several oxidants: air, oxygen, hydrogen peroxide, and calcium peroxide. Table 8-12 lists the roles and characteristics of different oxidants in the leaching process.
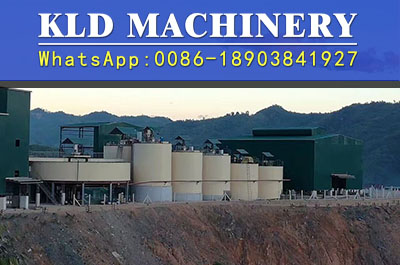
air |
Maximum oxygen concentration 9×10-6 It will volatilize the HCN gas from the solution |
oxygen |
Maximum oxygen concentration 40×10-6 Accelerated leaching kinetics: in the presence of active sulfides, cyanide can be saved and Pb (NO3) 2 dosage can be reduced. |
H2O2 |
Maximum oxygen concentration 40×10-6 Accelerated leaching kinetics: no volatilization of HCN in solution; dosage of NaCN 0.2-0.5 kg/t; reduction of cyanide dosage; increase of gold recovery rate |
CaO2 |
Maximum oxygen concentration 40×10-6 Improving gold recovery: accelerated leaching kinetics; no volatilization of HCN in solution; release of available oxygen at a moderate rate and a long effective time; amount of NaCN 0.1~0.8kg/t |
If the demand for oxidants is not high, the cheapest oxidant is compressed air. The position of the gas ejector in the tank has a great effect on the air efficiency. In order to dissolve oxygen fully, the air injection must be carried out in the high pressure area. The high pressure zone is located at the center of the impeller wing tip, where mixing is the strongest. The oxygen dissolution efficiency is much higher than that obtained by aeration from the low pressure area below the blade. The limitation of air filling is that with the increase of the amount of oxidant needed, the amount of cyanide loss from solution in the form of volatile HCN gas also increases, especially under the condition of low pH value and high salt content, the loss of cyanide is greater.
Oxygen is more suitable if the oxygen demand is greater. As the volume of gas in contact with the solution is greatly reduced, the amount of HCN volatilized from the solution is also greatly reduced, so the consumption of cyanide is significantly reduced. There may be a contradiction between the cost and benefit of using oxygen and compressed air, but compared with the increase of oxygen cost, the higher gold recovery rate and the lower consumption of cyanide will result in greater benefit due to the sharp shortening of leaching speed and the decrease of cyanide consumption.
Many remote cyanide plants with high oxygen demand can add hydrogen peroxide. Hydrogen peroxide is used to avoid the engineering problem of oxygen dissolution and the volatilization of HCN in solution. The amount of (PAL) H2O2 added in the typical hydrogen peroxide assisted leaching process is about 0.2~0.5kg/t. It is best to install an oxygen probe in the first dip tank to control the amount of H2O2 added. In some cyanide plants, the gold recovery rate was increased. Lee etc al. (1989) reported that the gold recovery increased by 7% and the cyanide consumption decreased from 1.7kg/t to 1.1 kg/t at PineGreek (N T) using 0.55kg/t H2O2. The concentration of dissolved oxygen in Fairview Mine in South Africa is very low because of the organic matter in the pulp. With the application of PAL process, the leaching rate of gold is increased from 61% to 73%, and the value of increasing the recovery rate is 6 times higher than that of the cost of PAL process.
If you require a slow release of oxygen from the added oxidizer, use calcium peroxide for this effect.This property of calcium peroxide can play an important role in heap leaching.Calcium peroxide is reported to be used in heap leaching to release oxygen continuously for at least 20 days.The leaching rate is still increased by adding calcium peroxide, and the final recovery rate may not be improved, but the cyanide consumption can be reduced.