Chemical treatment of Refractory Copper Ore-summary
2020-09-17 10:46Introduction:Chemical treatment of Refractory Copper Ore - summary Because of the poor floatability of the copper oxide minerals, especially when the copper in the ore is immovable malachite, hematite and ferric hydroxide, the copper deposit impregnat
Because of the poor floatability of the copper oxide minerals, especially when the copper in the ore is immovable malachite, hematite and ferric hydroxide, the copper deposit impregnated with aluminosilicate is either in the form of bound copper, and the copper mineral has a fine grain size. When the copper content is high and the ore slime content is much, it is difficult to obtain the ideal technical and economic index by flotation treatment. At this time, the copper can be recovered by chemical ore dressing process.
The refractory copper ore treated by chemical ore dressing process is that it is often deposited on the surface of many copper ore bodies and sometimes more developed oxidation zones; in some mines, a large number of copper containing waste stones (low grade copper ores) are stored in the early stage of large-scale exploitation; in the end of production, there will be copper residue that is unrecoverable, and some floatation plants are stacked with high grade old copper tailings, etc.
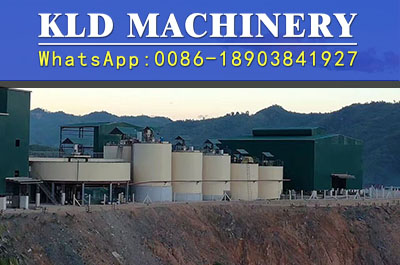
According to the characteristics of leaching solution obtained from decomposing copper ore and the requirement of product form, copper can be recovered from the leachate by iron replacement proces, precipitation-flotationprocess, direct electrodeposition process, extraction-electrowinning process and distillation-precipitation process, respectively. Separation copper is usually recovered by flotation.
According to the ore characteristics and specific conditions, leachate tank leaching, in-situ leaching, heap leaching and various agitation leaching processes can be used in leachingprocess. In-situ leaching and heap leaching are used to treat low-grade copper ore and waste rock, with long leaching period and low leaching rate, and leaching in leachate tank and agitation leaching are used to treat oxidized ore or mixed ore with copper grade of more than 0.5%, with short leaching period and high copper recovery rate. At the same time, the rich copper can be recovered directly by electrodeposition.
Common chemical treatment methods for refractory copper ores can be summarized as follows:
1. Leaching-replacement -electroproduct;
2. Leaching-extraction-electrowinning (LXE process) (including roasting-leaching - extraction-electrowinning);
3. Leaching, precipitation - flotation (LPE process);
4. Segregation -flotation process.