Process factors affecting the flotation process – processin
2020-11-18 10:15Introduction:Process factors affecting the flotation process processing fineness Any physical mineral processing method is to separate different minerals according to their type and properties.It first requires dissociation of the selected mineral mono
Any physical mineral processing method is to separate different minerals according to their type and properties.It first requires dissociation of the selected mineral monomers, and secondly, the most suitable mineral particle size is different due to different ore benefication methods.For flotation size, the maximum flotation size must not be exceeded.The upper limit of particle size varies with mineral density.The upper limit of flotation size of sulfide mineral is generally 0.3mm, while for those with less density, such as sulphur, graphite and coal, flotation size can be up to more than 1mm.Superfine size (less than 5μm) is also difficult to flotation.Moderate particle size is easier to flotation.So the grinding and flotation operators must often measure the overflow fineness of classifier.
The oversize grain often occurs in the mine feeding into flotation, possibly due to the lack of design capacity of the ball mill and the rising production task.It may also be due to the use of hydraulic cyclone and other classification efficiency is difficult to accurately control classification equipment, classification products "run rough."
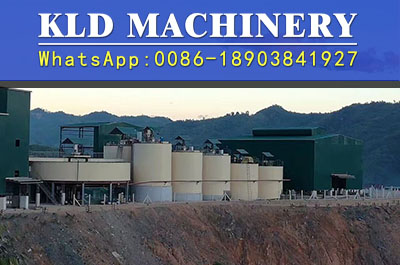
1. The available mineral and gangue mineral have not yet been dissociated.
2. The coarse particle move in the slurry and encounter turbulent turbulence, causing them to fall off the bubble.
In order to process the coarse particle, conditions conducive to the flotation of the coarse particles must be created, such as:
1. Sufficient collector to form good hydrophobicity;
2. Increase the filling amount air to form larger bubbles;
3. Under the condition of stable slurry surface, there is not too strong stirring or rising slurry flow;
4. Use higher concentration to increase the buoyancy of the slurry;
5. Designed foam tank shall discharge foam timely;
6. The side Angle and dead Angle of the tank body of flotation machine are less, which can reduce the coarse sand settling groove;
7. In some cases, flotation machines suitable for coarse particle flotation are selected.Such as shallow trough, with grid plate, floatation machine in the appropriate upward flow, application of foam separation flotation, boiling layer flotation, bench floatation , particle floatation and other equipment and methods.
The term "fine (ore) slime" generally refers to the fine grain level less than 18 ~ 10μm, but different upper limits are usually drawn for different plants and mines due to the limitation of the type of ore or the function of the equipment used.Fine slime flotation is a very important problem in flotation field.Because fine slime has three properties that are not conducive to flotation, that is, fine slime of a single particle has a small mass, larger specific surface area (the specific surface area per mass particles is larger) and unsaturated surface bond force is unsaturated.This makes the flotation concentrate low grade, low recovery and high consumption of flotation agent.
1. The effect of small mass is: small volume is less likely to collide with the bubble;It is difficult to overcome the resistance of the hydration layer between the mineral and the bubble when colliding with the bubble due to low mass and low kinetic energy.It also prevents the coarse particles from sticking to the bubbles.Light weight and slow sinking in the foam layer of the slurry, making the slurry and foam sticky, resulting in the decline of concentrate quality.
2. The effect of larger specific surface area is: they will absorb a large amount of flotation agents in the slurry, break the normal flotation process, and increase the consumption of flotation agents;Larger specific surface area also reduces the bubble's load capacity.
3. The effect of unsaturated surface bond force is as follows: the surface activity of the mineral slime is large, and it is easy to interact with various flotation agents, resulting in large consumption of flotation agents and even reducing selectivity;The fine slime has a strong hydration ability, which makes the slurry sticky. When the slurry with strong hydration ability is attached to the surface of the bubble, the water film on the surface of the bubble is not easy to flow away, making the foam excessively stable, which brings difficulties to the selection, concentration, filtration and other operations.
There are primary and secondary slime in ore benefication.Primary mineral slime refers to mineral slime formed by natural weathering in the deposit, such as kaolin, clay, etc.Secondary mineral slime refers to the slime produced in the process of mining, transportation, crushing, grinding and separation. Special attention should be paid to avoid the formation of fine slime by overgrinding.In general, primary mineral slime is harder to float than secondary mineral slime, and it is more harmful to the process than secondary mineral slime.
Some measures can be taken to mitigate the effect of fine slime on flotation.If the stage separation process is adopted, the ore particles which have been separated from the monomer will surface in time to avoid regrinding.When there is a large amount of mineral slime, the slurry can be flotation with relatively thin slurry to reduce the slurry viscosity.In order to reduce the absorption of fine slime to the flotation agent, the process of subsection flotation agent can be adopted. Sometimes, a small amount of foaming agent and a small amount of collector are used to schweben some fine slime, and then the flotation agent is added for formal rough flotation .Dispersants may be added if necessary to reduce their impact.When the amount of slime in raw ore is large (such as -0.074mm yield is higher than 15%), hydraulic cyclone should be used to remove mineral slime, and then slime and sand separation should be carried out.
In the solid-liquid interface, mineral processing methods for dispersant, coagulant, flocculant and some fine slime have been introduced, which can be used as appropriate.Only one or two examples are presented here.
After grinding the iron ore in a certain place in China, the sodium humate is used as a flocculant for selection of flocculation. As the sodium humate only flocculates hematite together, the flocculation of quartz and other gangue is basically avoided. After flocculation, the grade can be doubled.
"Shear flocculation" is also used in scheelite flotation to improve the recovery rate of fine grain scheelite.It is to conduct high speed stirring after the ore pellets are hydrophobic with oleic acid and other collectors to strengthen the flocculation of the superfine white tungsten ore at about 10~ 40μm.Even though all particles have a high negative charge, their flocculation is strong.This kind of flocculation is actually a fine slime at 1 μm covering the coarse particles at 10 ~ 40μm.There are two basic conditions for such shear flocculation to occur:
1. The average collision kinetic energy obtained by strongly stirred particles is far greater than its thermal motion energy, and the force of particles close to each other force is greater than its dispersed force;
2. The association of hydrophobic base contributes to the formation of flocs. It can be seen that the bridge flocculation caused by shear flocculation is different from the bridge flocculation caused by the electro polymer or high polymer caused by the compressed double-layer.High mixing intensity is very strong for shear flocculation, but it is not good for the survival of electropolymer and bridge flocculation.
This superfine particle attaches to the coarse particle flotation, also known as loading flotation.Loading flotation has been used to separate anatase from kaolinite.In flotation, calcite, which is thicker than anatase, is used as the carrier. In the case of tal oil and fuel oil, strong stirring is applied to make the fine anatase adhere to calcite.
In the process of sewage treatment, the vacuum foaming process or electrolytic foaming process can be used to produce very fine microbubbles as the carrier to float the fine mud in the sewage (see section 13.4).