Flotation development profile
2020-11-12 11:53Introduction:Flotation development profile In the ancient gold and silver panning process, it was realized that the natural hydrophobicity or hydrophilicity of minerals was used to purify the mineral raw materials.However, the emergence of flotation as
In the ancient gold and silver panning process, it was realized that the natural hydrophobicity or hydrophilicity of minerals was used to purify the mineral raw materials.However, the emergence of flotation as an industrial-scale ore beneficationing proocess abroad was around the end of the 19th century, when western countries developed rapidly and needed more mineral raw materials.
In order to recover useful metallic minerals from massive piles of reprocessed waste tailings, as well as concentrate products from fine leached lean ores or complex polymetallic ores, the flotation process has been developed and perfected.Especially in recent decades, with the successful discovery of many new flotation agents (surface active substances first) and the rapid development of modern industry, the flotation industry has also made great progress.
1. Total oil flotation process
A large amount of oil and slurry is mixed according to the different hydrophilic and hydrophilic properties of various minerals, and then the oil-wet mineral (such as sulphide mineral) adhered to the oil layer is scraped out, while the hydrophilic mineral (gangue mineral) remains in the slurry to achieve the purpose of separating the mineral, which was also the pioneer of early industrial flotation.The use of viscous crude oil to separate sulfide minerals from gangue was patented in 1860 and used in the production of copper sulfide ores containing precious metals.Another patent appeared in 1886. It was proposed that in addition to adding a large amount of hydrocarbon oil to mineral slurry as flotation agent, sulfuric acid could be added to mineral slurry containing a large amount of carbonate to produce bubbles, so as to improve the separation effect of sulfide mineral and gangue mineral.
In 1902, the "mass process" was proposed on the same principle as above.The process is characterized by adding a relatively small amount of oil (about 2% ~ 4% of raw ore) and the use of soaps to enable the selective flocculation of sulfide minerals in the slurry to form larger aggregates.As the gangue in the slurry does not work with oil and soap, the dispersed gangue can be washed away with water to separate from the aggregates.
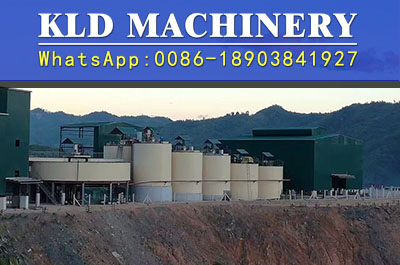
2. Surface flotation process
Surface flotation process in industry application appeared in 1892, its characteristic is to grind fine powder ore (such as copper sulphide) carefully flow gently over the water surface, then not easy wetting by water hydrophobic sulfide ore grain supported by the surface tension and floating on the surface of the water, and gathered into sulfide mineral thin layer, after collection to concentrate;Hydrophilic gangue minerals, which are easily wetted by water, sink into the water and are discharged as waste tailings.
In order to improve the floatability of sulfide minerals and make the separation process more effective, a small amount of hydrocarbon oil is added to the surface flotation process (e.g. 1/5000 of raw ore amount), and more than 300,000 tons of zinc concentrate were produced by this process in 1940.
Although the surface flotation process used a small amount of oil, but the mechanical equipment production capacity was small, the process technology was simple, and the gas-industry surface of separation was small and low efficiency, which was later replaced by the foam flotation process.
3. Foam flotation process
In order to improve the efficiency of flotation separation and reduce oil consumption, foam flotation process using air bubbles as mineral carrier and increasing gas-liquid separation interface is proposed.
In 1877, a patent for the foam flotation of the graphite ore was issued.Mix the ground ore with about 1 to 10 percent paraffin oil or grease (as per raw ore), then boil it with water until the vapor bubble causes the graphite particles emerge to surface.However, people did not realize the importance of using bubbles as sorting interface and ore pellet transport carrier at that time. It was not until the patent of using acid and carbonate mineral to produce bubbles for flotation appeared in 1886 that people clearly recognized the role of bubbles in the process of flotation and many processes of generating bubbles appeared successively.After replacing the oil droplet with air bubbles as the carrier of ore particles, a patent of using less than 8kg/t ore appeared, and later it was reduced to about 120-800g/t ore. Subsequently, it was found that the flotation performance of different oil substances was not identical.
In the early 20th century (1901), the more primitive foam flotation process was first adopted in Australia, which was used to treat abandoned tailings (mainly zinc blende) with a grade of up to 20% accumulated over the years, and produced more than 6 million tons of zinc concentrate with a grade of up to 42%.The process is characterized by dry tailings containing a carbonate gangue materials, in the hot dilute sulphuric acid solution, due to chemical reaction produces CO2 bubbles and the oil effect of sphalerite adhesion in CO2 and carried to the mineral surface, bubble surface scrape after a quick (zinc concentrate) foam products, this is the so-called chemical process to create a bubble "gas flotation process".A similar gas flotation process was used in Italy around the time of unification.
Air bubbles are used to increase the gas-liquid interface and carry the ore particles to rise, which makes the floatation process take a step forward greatly, and there are many forms of foam floatation process, among which the following are mainly:
⑴Gas flotation process(as above)
⑵Electrolytic flotation process.Electrolysis of water to produce gas was proposed in 1904, but was not used in industry.At present, it has been used in the purification of industrial wastewater and the production of waste water of some light and food industrial products and study the new technology of micro-bubble flotation of fine mineral.
⑶Vacuum flotation process.This process was introduced in 1904 and has been widely used in industry.The essence of the process is that the gas is pumped on the ore liquid to create a vacuum, which causes the gas originally dissolved in the ore slurry to separate out in the form of bubbles.
⑷Positive pressure flotation process.This process first pressurizes the slurry to facilitate air dissolution, and then reduces to normal atmospheric pressure, causing the dissolved air to release as bubbles.But it was not officially used in industry.At present, it has been widely used in new type of gas precipitated floatation machine.
⑸The air flow is pulverized with a mechanical stirrer to produce steam bubbles.In 1906, the patent appeared that the impeller was used to mix the slurry violently, and air in the atmosphere was directly inhaled to produce air bubbles for flotation. In 1910, mechanical agitating floatation machine appeared.When the mechanical agitation type flotation machine impeller speed is not high (only 300 r/min), but due to the rapidly rotating impeller in the pulp, form "funnel" air around the axis, in the center of the impeller at the same time form the negative pressure, so the atmosphere in the air after the "funnel" air drawn into pulp, and the agitation of the impeller diffuse into small bubbles.Later, oil produced some air-lift floaters, which were either pumped directly into the air by perforated bottom plates (1914), or pumped directly into the air by pipes immersed in the slurry.
The above processes and equipment for generating air bubbles, in addition to chemical processes for generating air bubbles, are subject to the limitations of mineral conditions. In particular, several other processes have developed in modern times, in particularin the recent 20 years, flotation equipment has been constantly updated, and increasingly large and diversified.