Example of foreign carbon in pulp plant - South African Pres
2020-10-27 10:32Introduction:Example of foreign c arbon in pulp plant - South African President Brand baking sand carbon in pulp plant This plantdeals with roasted sand.The production scale is 900 ~ 1000t/d, thefinenessof baking sand is 95-200 mesh, containing 10 ~ 12
This plant deals with roasted sand.The production scale is 900 ~ 1000t/d, thefineness of baking sand is 95-200 mesh, containing 10 ~ 12g/t of gold.Completed and put into operation in August 1980, it is the first large carbon in pulp plant in South Africa.The successful experience of this plant has played a positive role in promoting the wide application of carbon in pulp process in South Africa.
Process description:
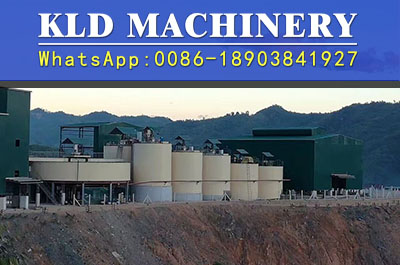
Table 9.1-1 leaching conditions at President Brand baking carbon in pulp plant
Leaching conditions | actual numerical |
siurry density /t·m-1 Slurry concentration (solid)/% Leaching time /h pH value temperature /℃ Cyanide concentration /% Calcium oxide concentration /% |
1.46~1.54 50 6~7 10.0 In the summer 30~35 In the winter 20~25 initial 0.04 last 0.038 0.01~0.017 |
The desorption process adopts AARL process.Pretreatment: with5% NaCN + 1% NaOH solution at 90 ℃ for 30 minutes to gold-loaded carbon.Desorption: with three times the carbon bed volume of soft water desorption 1.5 h, the temperature is 110 ℃.
Pickling is done in the desorption column before desorption work begins.Use twice the carbon bed size, the concentration of 3% dilute hydrochloric acid under the temperature of 90 ℃.The existing problem is that the CO2 generated by the reaction fluidizes the carbon particles and transports the carbon to the top of the desorption column, causing blockage of the outlet screen and increase of the desorption column pressure.
Carbon regeneration is carried out in a Wellman regeneration kiln heated by electricity.The length of regenerative kiln is 9.0m, the length of heating zone is 4 ~ 5m, and the length of cooling zone is 3 ~ 4 m.Heating zone temperature control at 700 ℃, the discharge of carbon regeneration temperature is 150 ℃.It is cooled by air from the outside.Carbon regeneration time is 20 minutes.
The electrodeposition loop includes 3 AARL shaped deposition tanks made of polyvinyl chloride, two working and one standby.Process pregnant solution 13 ~ 18m3 per day.A Dupont NAFION 420 cation exchange membrane is arranged between the cathode and the anode of the deposition tank.About 40% ~ 50% of cyanide in the cathode can be regenerated and returned to the leaching circuit for use.The anode electrolyte used contains NaOH 20%-25%, and the electroproduct parameters are shown in table 9.1-2.
Table 9.1-2. electrodeposition parameters of President Brand baking sand and carbon in pulp plant
parameters | unit | Design value | actual numerical |
Pregnant solution grade Barren solution grade recovery rate flow Cathode solution temperature Anode solution concentration electric current intensity Cell voltage electrodeposition time |
g/m3 g/m3 % m3/h ℃ % A V h |
900 20 97.8 4.8 50 25~30 24 |
716.4 21.8 97.0 3.8 50 24 180 5.2 16 |
The cathode steel wool from the electrodeposition tank is dried and then mixed with borax to be smelted in induction furnace.